Digitisation can simplify production processes, making them more efficient and removing the need for excessive paperwork. In this interview, Hanspeter Groth, Industry Leader Manufacturing at Swisscom, explains how to approach a shopfloor digitisation project and the role played by low-code development.
Mr Groth what do we mean by digitisation in the manufacturing industry?
There are two layers. Firstly, the horizontal production process on the shopfloor can be digitised, from the raw material to the end product and its use by the customer. This often still results in media discontinuity. The production process itself may be partially digitised and paperless. Once the product leaves the shopfloor and is transported to the warehouse, to a further product level or to the customer, the processes are not fully digitised, and you have to work with paper documents again.
And the second layer?
This is about the vertical integration from top floor to shopfloor. Top-floor systems, such as ERP and PLM (product lifecycle management) are used in the planning process to determine what should be manufactured and when, the quantities required, where the materials are from, etc. This data needs to reach the shopfloor “downstairs” as directly as possible, and this can be problematic in many industrial companies.
Can you give an example?
A production employee receives order data from the ERP. They may then need to read certain machine data and enter it manually, as well as transferring other information, such as quality data, to other systems. In this case, there is potential for digital development in both directions, both vertically and horizontally.
‘Low Code can demonstrate its advantages in many scenarios, whether for the digitalisation of entire production processes or for individual production steps.’
Hanspeter Groth
Why isn’t the shopfloor digitised yet?
It is relatively straightforward for manufacturers of standard products with large production runs, such as refrigerators or valves, to digitise their production. The manufacturing process is standardised, meaning that the hurdles to digitisation can be overcome. However, there is a growing trend towards customised products with a single production run, where each product has a different manufacturing process and the customer requests last-minute changes.
What problems does this cause?
It becomes difficult to maintain an overview and to guarantee quality. The more individual a product needs to be, the more complex it is to digitise. The question then is whether the benefits justify the costs.
Is there evidence of the trend towards customised manufacturing?
Yes, it is quite clear. The University of St. Gallen’s Swiss Manufacturing Survey 2022 demonstrates that, among the 308 Swiss industrial SMEs and large corporations surveyed, there is a strong focus on customised products, which they manufacture in line with the engineer-to-order (30%), make-to-order (29%) and assemble-to-order (15%) models. Only 26% of the firms have an exclusively make-to-stock model, where stock items are manufactured independently of customer orders.
Are there other challenges?
Many companies have machinery from different generations, often decades old, which is a challenge. Some of the brown-field equipment of this nature is not equipped with digital interfaces. Alternatively, it may work with a wide range of interfaces and data protocols and be very complex to integrate. Location also has a part to play. It is easier to digitise a centralised production facility at a single site than distributed manufacturing across ten different factories. This is especially true when different machinery and employees with different expertise are deployed at these different locations.
How can ERP and PLM be combined with the shopfloor?
A strong, well-considered overall design, which includes not only technical aspects but also factors such as data governance and cyber security, is crucial. Without this big picture, it won’t work. The optimum technology can then be determined on the basis of the overall design. If you take something that already exists (e.g. by expanding the ERP or PLM solutions), you can rollout a comprehensive MES solution (manufacturing execution system), or you can take new approaches, such as with low-code.
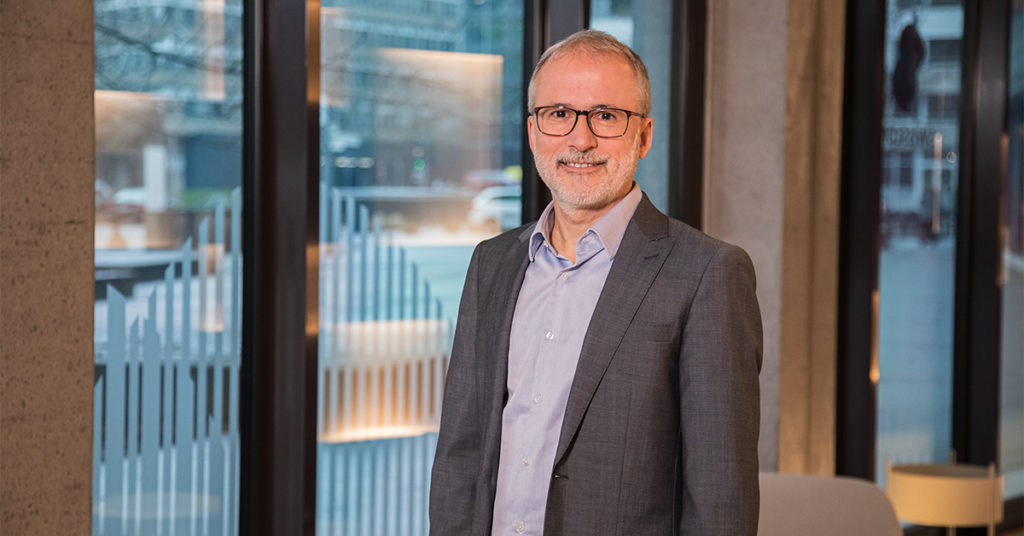
We hear low-code all the time: what does it mean?
Today’s low-code tools can be used to digitise and simplify processes, thus automating repetitive tasks. To a large extent, the development uses drag-and-drop designers without the need for complex program code. Excel-style formula languages map the necessary business logic. In keeping with the democratisation of digitisation, this means that process-oriented employees with no programming knowledge can actively accelerate the digitisation process. In a time when IT specialists are thin on the ground, this is an attractive proposition.
What are the practical applications of low-code platforms on the shopfloor?
Low-code platforms allow production processes to be digitised in a straightforward way and remove the need for paper. Low-code can prove advantageous in a number of scenarios, both in the digitisation of entire production processes and at individual stages of production. Low-code platforms not only contribute to easier data entry and improved data quality. They also serve as a data hub between the systems involved, including adjusting data structures during transport. As a result, low-code also creates the basis for data evaluation and complex analyses.
Digital Manufacturing Services
Industry leaders have increased their productivity by up to 90% through digital transformation. Swisscom specialists support you in the digitalisation of production.
What are the specific benefits of low-code?
Low-code platforms help to accelerate digital transformation. With a shorter time-to-value, they have a significant impact on the cost-benefit analysis of every digitisation project.
What are the low-code platforms out there?
The market for low-code in the industrial sector is not complex. Two of the main providers are Mendix and Microsoft. Of these, Microsoft’s Power Platform has enjoyed particular early success in the market. Power Platform offers outstanding options for integration with Microsoft 365, Dynamics 365 and Microsoft Azure. Integration into the Microsoft Teams collaboration solution unlocks particularly creative options. Hundreds of connectors are available to integrate heterogeneous system landscapes into SAP, Oracle, ServiceNow and Salesforce among others. Proprietary and in-house solutions can also be connected using generic interfaces or automated via RPA using synthesised inputs.
What is the process for rolling out a low-code platform?
Low-code is particularly suited to the rapid implementation of individual use cases within the rapid prototyping model. This allows the customer to understand the advantages of low-code in a live environment. Governance principles are crucial to ensure that any scaling of the use case at a later stage remains under control. This will strengthen the platform’s security and compliance and integrate it into the company’s standards.
Are there any other considerations?
When low-code is used strategically within the company, a centre of excellence must also be established to monitor activities on the platform and support the scaling process. A leverage effect will occur soon after a successful rollout and additional use cases can be built on what has been achieved. Active low-code portfolio management controls that development effectively.
What are the limits of low-code?
There are virtually no limits to what can be achieved with low-code. However, the specifics of the use case or the sector in question will determine whether it is the ideal solution in all cases. If compliance with complex regulatory requirements (audit trails) is needed, it may be better to purchase a specialised solution. The same applies to unusual or proprietary requirements. If in doubt, conventional software may be the best option. It should also be noted that low-code, standard solutions and conventional software development can be combined and are not mutually exclusive.
Can you give an example of a Swiss low-code project?
A prime example is Geobrugg AG, a global manufacturer of solutions to protect against natural hazards, such as rockfalls, earthquakes and avalanches. The company previously used an error-prone, time-consuming solution based on numerous Excel files for reporting machine data. Geobrugg now uses a low-code app based on Microsoft Power Platform, which was developed with the support of Swisscom. This simplifies the recording and validation of machine data. The data quality achieved allows complex analyses and forecasts to be carried out directly in the Azure Cloud.
How does Swisscom support the use of low-code to digitise manufacturing?
We offer support in terms of strategic direction, practical implementation of the use case on the low-code platform, strengthening the platform’s data governance and change management. We take a technology-agnostic approach to this and work with the customer to find the right solution. This may include other technologies alongside low-code. We also focus on SAP-centric system landscapes. Swisscom can adapt these to the needs of the customer or take over their operation. And Swisscom can also provide an independent second opinion on projects that are already planned.